Choosing a washing machine is not an easy task, because in addition to the appearance and dimensions of the device, it is necessary to take into account many other characteristics. In particular, the most important selection criterion is the washing machine motor. Each of them has its own advantages and disadvantages.
The design and principle of operation of the washing machine engine
As a rule, the washing machine motor is fixed at the bottom. Only one type of motor is installed on the drum - inverter.
The commutator motor is the most common, so the principle of operation will be discussed on it.
The collector consists of a copper drum divided by partitions into several sections. The brushes supply current to the armature, which, in turn, creates a magnetic field, due to which rotation occurs.
Rotation continues as long as voltage is supplied to the motor. At the same time, the speed is significantly affected by the voltage in the network.
Types of engines
Currently, the washing machine market is represented by 3 types of engines:
- asynchronous (obsolete);
- collector (the most popular);
- inverter (the most modern).
At the same time, all engines have advantages, disadvantages and distinctive technical features.
Asynchronous motor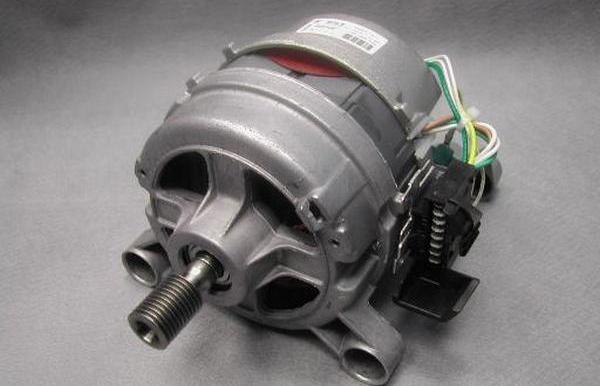
Such motors come in three- and two-phase types, but the latter are practically not produced at present. They consist of a rotor and a stator. Rotation is provided by a belt connected to the drum. The motor can provide up to 2.8 thousand revolutions per minute.
Advantages of asynchronous motors:
- low price;
- ease of repair and maintenance;
- low noise level during operation.
To care for the engine, it is enough to change the bearings and periodically renew the lubricant.
It is worth noting that in modern washing machines this type of motor is not used due to low efficiency and difficult control of electrical circuits. They are used only in budget models.
Brushed motor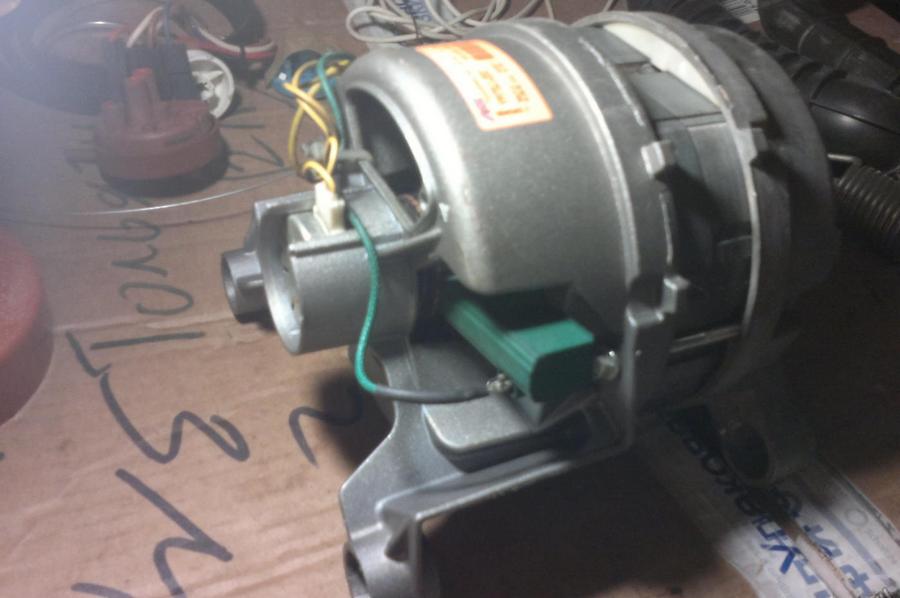
This type of motor is used in most washing machines. It consists of an aluminum housing, several brushes, as well as a rotor, stator and tachometer.
The motor can have 4, 5 or even 8 pins. Brushes are necessary to ensure contact between the motor and the rotor.
The motor is located at the bottom of the structure and is connected to the pulley using a belt. This leads to the main disadvantage of this engine - severe wear of some elements, leading to breakdown of the washing machine.
The advantages include small size, simple electrical circuit, lack of frequency reference, fast speed and easy repairs.
Inverter motor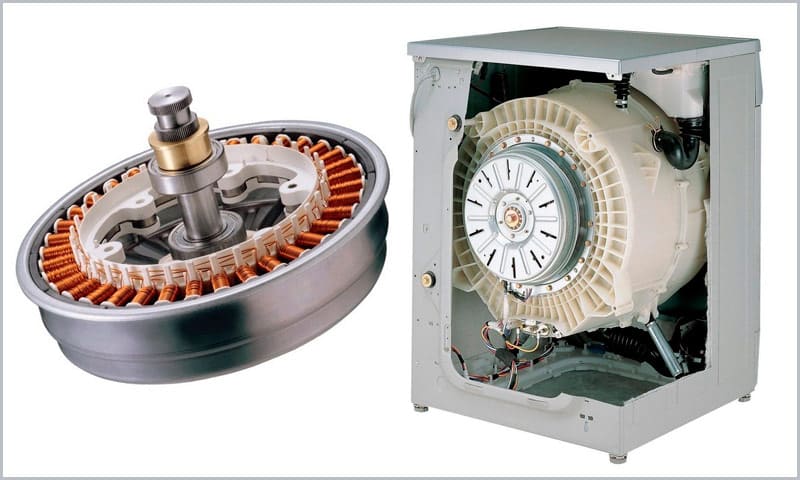
The inverter is a cover equipped with magnets and a cage with coils.The key feature of this type of motor is the absence of brushes and a transmission belt, since the inverter is integrated directly into the drum.
There are 2 ways to place rotor magnets: inside the stator and outside. Washing machines use the latter type. During engine operation, voltage is supplied to the windings, undergoing conversion to inverter form.
Thanks to these features, it becomes possible to control and change the speed of revolutions.
Among the advantages of this technology are the following:
- simplicity of design;
- small dimensions;
- absence of wearing parts;
- low energy consumption;
- low noise level during operation;
- minimal vibration during spinning.
The inverter motor does not need to overcome friction to operate. This feature reduces energy costs. However, the level of savings is small (about 5%).
Thus, the inverter motor has high power and high efficiency despite its small dimensions. At the same time, the design is highly reliable due to the minimum number of connecting elements. But such engines are not cheap, since their production is not cheap.
Which engine type is better?
Although all types of motors have advantages and disadvantages, the main competitors are inverter and brushed motors.
It may seem that the choice is obvious and the advantage is on the side of the inverter motor, but not everything is so simple.
Manufacturers describe the technical characteristics of their products in some detail in the instructions.However, the user may not understand enough about the specifics of the operation of washing machines and exaggerate the importance of some indicators, which in fact act more as a marketing ploy than a real advantage compared to other models.
For example, when advertising washing mashines with inverter motors, you can hear that energy savings, compared to collector ones, are about 20%. In reality, the situation is slightly different, since the main consumption of electricity is not from the motor, but from the tubular electric heater, which heats the water.
As a result, the user can really save money, but only with a small load of laundry and incomplete spin-up of the drum. In real conditions, energy savings will range from 2 to 5%, and during full load they can be completely reduced to zero.
Another advantage of the inverter motor is the low noise level during operation. The brushed motor is indeed noisier due to the presence of brushes in its design, but the inverter motor makes squeaking and whistling noises.
It is worth noting that, in addition to the engine, the drum, as well as the pump responsible for drawing and draining water, makes noise in the washing machine.
When purchasing, attentive people will also pay attention to the speed of revolutions. Inverter motors boast a speed of 2000 rpm, but are such high speeds really needed? If a person dreams of almost dry laundry after washing, then yes. But even here there were some nuances. So, at a high spin speed, things very quickly become unusable, and some things, for example, wool, are not at all suitable for strong spinning. Therefore, after washing, the item will become unusable.
Also, the inverter motor is positioned as more durable. As a rule, when purchasing equipment, users do not expect it to last more than 15 years. It is important to note here that manufacturers set a service life of 10-15 years for brushed motors.
Many people worry about the wear of brushes, but their durability remains at an acceptable level. So, with a daily two-hour load, their service life is up to 15 years. Moreover, even if they do wear out, the cost of replacement is very insignificant.
Experts involved in repairing washing machines claim that, according to statistics, bearings, tubular electric heaters and control units fail much more often.
It is worth paying attention to the design feature of the inverter motor: the joint location of the motor and the drum. On the one hand, there are no additional loads in this design, but there is also a significant disadvantage. So, if the oil seal breaks due to the close proximity of water and the electrical part, the winding may burn out.
Some manufacturers claim that there are no rubbing parts, but this is no longer a marketing ploy, but a lie. There really are no brushes in the inverter motor, but there are bearings. At the same time, their service life and degree of wear do not differ from other types of motors.
The warranty on inverter motors is up to 10 years, but for other parts of the washing machine, manufacturers provide a guarantee from 3 to 7 years, and the cost of repairing such motors is very high.
Therefore, it is impossible to definitively answer which engine is better. Often, the benefits of an engine end up being a marketing ploy or even an outright lie.
How to check the performance of the motor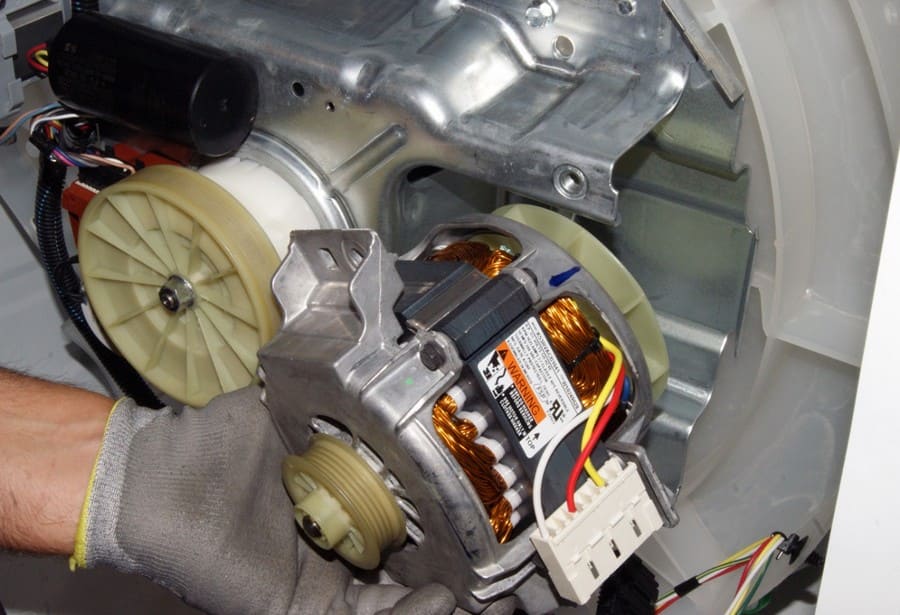
Checking the performance of an inverter motor without the help of specialists is very difficult. The easiest way in such a situation is to run a self-diagnosis, which will determine the malfunction and notify the user about it using a special error code.
If, nevertheless, there is an urgent need to check the performance of the engine, then its dismantling must be performed in a certain sequence.
First, you need to unplug the washing machine and remove the back cover by unscrewing the corresponding fasteners. Next, you need to unscrew the screws that hold the wiring, and then the bolt that secures the rotor. Then you need to dismantle the rotor and stator and remove the wiring connectors from the stator.
After this, you can begin to inspect and test the engine.
It is much easier to check the performance of a commutator motor. This can be done in several ways, but first you will have to dismantle it.
To do this, you need to unplug the washing machine and remove the back cover. Then you need to disconnect the wires from the motor and remove the fasteners.
Next, you need to connect the stator and rotor windings, and then apply 220 V. To avoid a short circuit, you can connect a tubular electric heater in the form of ballast. This is done to protect the engine from combustion. If the motor rotates and the tubular electric heater gets very hot, this indicates a possible short circuit in the windings.
There is nothing to repair in an asynchronous motor yourself. Malfunctions that can appear in this type of motor are due to problems with the stator or rotor windings. Only professionals can fix such a malfunction.
The most common causes of washing machine motor failure
One of the most common causes of commutator motor failure is faulty brushes. Their malfunction may be indicated by a loss of rotational force of the drum and an increased noise level during operation.
Overloading the tank is the most common cause of brush failure. They also become unusable quite quickly if you use the spin cycle at maximum speed. Do not forget about the belt, which can come off the pulley or even break.
A visual inspection can also help determine the need to replace brushes. So, if they spark during operation or have a black coating, then they need to be replaced.
If this element malfunctions, repairs can be carried out at home. To do this you need to buy a suitable model. It would be best to buy an original set from the manufacturer.
Another common cause of breakdown is faulty lamellas. These plates wear out quite rarely. The cause of the malfunction may be a broken cord in the winding.
As a rule, this is due to improper operation of the washing machine. For example, starting the washing process with the drum doors open.
If the problem is with the plates themselves, then the rotor is most likely beyond repair. However, if the peeling is minor (about 0.5 mm), then you can turn the rotor on a lathe. To do this, you need to fix the rotor and sharpen the lamellas, aligning them in thickness. Then carefully clean off dust and shavings.
The presence of this malfunction can be determined by turning the rotor. This will be indicated by the appearance of a characteristic sound.
Also, engine malfunctions may be associated with a break or short circuit in the winding. This may be caused by the following:
- overheating of the motor housing due to short circuits in the winding;
- winding insulation failure.
You can detect a break using a multimeter. To do this, you need to switch the device to resistance measurement mode and check the resistance between the lamellas. The norm is an indicator value from 0.1 to 0.4 Ohm.
Due to a short circuit in the motor, other elements of the washing machine may also become unusable. For example, command apparatus, reverse relay and others.
Thus, in most cases, washing machine motor failures occur due to non-compliance with operating rules, as well as due to instability in the electrical network. In order for the device to work longer, you must strictly follow the operating rules described in the instructions. It is also advisable to use a differential circuit breaker to protect the washing machine from power surges.
Washing machine motor connection diagram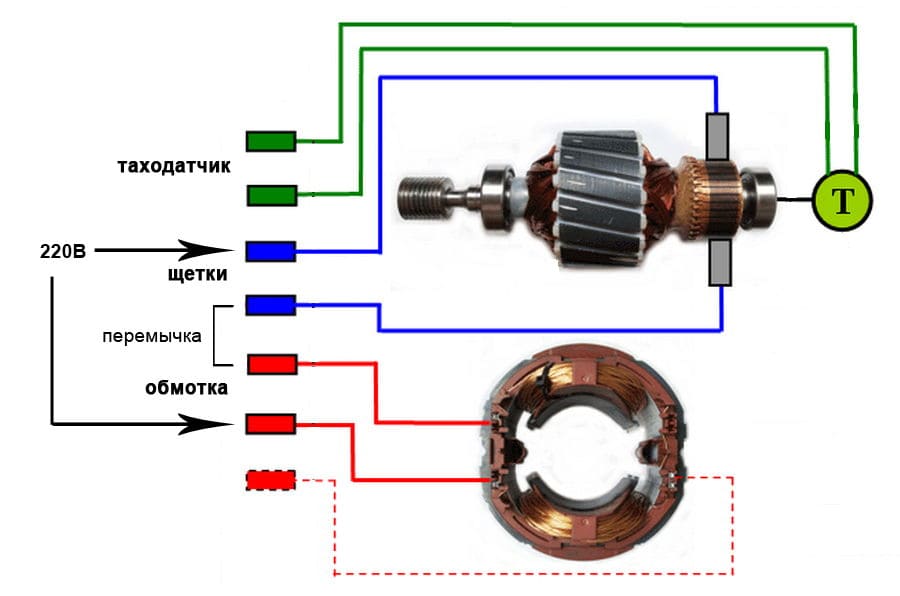
Typically, modern brushed motors can operate on both direct current and alternating current. In this case, the motor does not need a starting winding, and a capacitor is not required to start it.
To start the motor, you need to connect the wire to the network. It is worth noting that it is better to first study the technical data sheet to find the necessary information.
The motor can have from 5 to 8 leads, but they are not needed for operation outside the washing machine. First you need to eliminate unnecessary tachometer contacts. The resistance value on them is approximately 60-70 Ohms.
The motor will rotate in one direction if you perform the following steps: first connect voltage to one of the winding terminals, then connect the second terminal to the first brush, and connect the second brush to the voltage wire.
If you change the connection of the brushes, that is, swap them, the engine will begin to rotate in the other direction. In this case, the first brush must be connected to the network, and the second one must be connected to the output of the winding.
To check the engine, you can use a 12-volt washing mashine battery. As a result of incorrect connection, the engine will not burn out, since the battery voltage is low. In addition, at low voltage you can observe the operation of the engine at low speeds.
When a voltage of 220 Volts is applied, the engine starts abruptly, with a jerk. To avoid damage and short circuits, the motor should be securely secured and stationary.
You can use a dimmer to adjust the engine speed. When choosing it, you need to focus on power. The dimmer power must be greater than the power of the washing machine motor.
How to extend engine life?
Compliance with operating rules and careful handling of the washing machine significantly increases its service life, and also reduces the likelihood of failure and the need for repairs.
When connecting the washing machine to the network, you need to carefully select the wires. So, you cannot use a two-core aluminum cable for power supply, but you should use a copper and three-core cable.
A circuit breaker can be used to protect the line. In this case, its rated current value should be 16A.
Since not all houses have grounding, you need to do it yourself. To do this, you can separate the PEN conductor and install a grounded socket. The ideal option would be a socket with ceramic fittings and a higher protection class. This is especially important if the washing machine is located in a room with high humidity.
It is advisable to avoid the use of tees, extensions and adapters. If voltage drops occur quite often, then it is recommended to connect the washing machine through a converter. A good choice in this situation would be a residual current device. In this case, its parameters should not be higher than 30 mA. It is best to provide power to the washing machine from a separate group.
Under no circumstances should the washing machine body be grounded together with heating or water pipes. Also, children should not be allowed to play with the control panel buttons.
You cannot change the program during washing. If the device has mechanical control, then do not turn the switch counterclockwise.
And a few more important rules: do not overload the drum during washing and do not set the spin speed to the maximum value.
Conclusion
Thus, each type of engine has its own advantages and disadvantages. It is necessary to choose a washing machine based on the requirements for it and financial capabilities.
So, if you manage to allocate enough money to buy a machine, then it is better to take a device with an inverter motor type. If you don’t have enough money to buy an inverter or the overpayment seems impractical, then you can buy a washing machine with a commutator motor.
After all, the brushes that many people worry about don't wear out that quickly, and the cost of replacing them is negligible. At the same time, other elements, which are also present in inverter machines, break more often.
It is important to follow the operating rules and treat the equipment with care, and then it will serve for a long time.