Knowing the meaning of the Bosch washing machine error code, the user can either fix the problem himself or report the code when calling a technician to accurately describe the problem. The following is a list of errors and their meanings.
F01
Interference when closing the hatch. An indicator with a “lock” lights up on the machine panel. The wash does not start. Most likely, the hatch does not close due to debris getting into the lock, a deformed seal on the door, or clothes sticking out of the drum. If there are no visible obstacles to closing, then the following solutions are possible:
- replace the locking mechanism;
- reflash the module;
- replace the faulty processor.
F02
There is no water supply to the machine. Washing does not start or stops after a short time. The first step is to check the presence of water (there is pressure, taps, risers are not blocked). If the pressure is normal, you should restart the machine after checking the water supply hose. Perhaps it is pinched by something.
If the error occurs again, you need to check the water purification filter located on the water intake hose. If these steps do not help, the water supply valve or pressure sensor must be replaced. You may have to reflash the board.
F03
The water is not drained after washing.Occurs if within 10 minutes after the end of the program there is still water inside the machine. The laundry remains wet and not wrung out. Causes that can be eliminated on your own:
- There is a blockage in the sewer pipe, filter or hose.
- Incorrect hose installation level (too high or low).
If there are no blockages, the hose is located at the desired level, then:
- The drain pump or pressure sensor is faulty.
- The control module is faulty.
F04
Leak. Instead of draining, the water gets under the machine. It is necessary to check all hoses, filters, and seals related to the drain. One of them is leaking or not tightly connected. You should also check the hatch seal, it may be damaged or dislodged. If necessary, replace damaged parts to eliminate the cause of the leak.
F16
The hatch is not blocked. Depending on the model, the error code or number of revolutions will flash on the panel: 800 or 1000. Occurs when the door fastening is displaced, the lock is damaged or the locking tab is displaced. In most cases, damaged parts must be replaced, but it is possible to correct the problem by tightening the bolts. The cause of the error may be a failure in the electronic module.
F17
Exceeding the time interval allotted for collecting water. Occurs:
- When turned on: the door is locked, but no water is drawn in.
- When executing the program: the machine freezes while drawing water and after a while issues the specified code.
- When rinsing: no water comes out.
On models without a display, the Rinse Stop and RPM icons will flash. Reasons for the error:
- the water is turned off or its pressure is too weak;
- the hose is pinched;
- the drain hose is not connected correctly;
- the filter is clogged;
- the fill valve or water level sensor is damaged;
- The control unit or its firmware is faulty.
F18
No water drainage. The drain pump may be faulty, the drain filter may be clogged, or the control board is damaged. The machine stops after completing part of the program. Repair: you need to turn off the power to the machine, then check the filter, straighten the hose, make sure there are no obstructions to the drain, check the wiring of the control module.
F19
No water heating. Occurs when there is no voltage in the network, scale appears on the heating element, damage to the temperature sensor or control board. First you need to check the voltage; if it is sufficient, you will have to service the heating element, heat sensor or board. The board may have hardware damage (burnt out contacts) or a firmware malfunction.
F20
Unscheduled water heating. The water is heated, regardless of the selected mode. Heating is carried out even when selecting a low temperature mode. Causes:
- The heating element, temperature sensor, timer are faulty.
- Software glitch.
You can fix the problem yourself by restarting the machine. If the problem is not solved, it is necessary to repair or replace one of the above technical devices or re-flashing the software component of the module.
F21
The drum does not rotate. Occurs for one of the following reasons:
- Broken or stretched drive belt.
- Broken brushes in the machine motor.
- Damage to the machine motor.
- Bearings are damaged.
- The movement of the drum is blocked by a stuck foreign object.
- Firmware failure.
If the error does not disappear after switching off and then on, then repairs are required: replacing brushes, belt, servicing the motor, disassembling the housing in order to find and remove the object blocking rotation.
F22
Water heating stopped. During the program, the machine stops without finishing heating the water to the desired temperature. Causes:
- Pressure drops in the water supply system - the water pressure is weak or inconstant.
- Power outage.
- Failure of the thermistor, level sensor or control board controller.
It is necessary to ensure constant water pressure and the required power in the power supply system. If the problem is not solved, then you should service the thermistor, board or level sensor.
F23
"Aqua-Stop". The "Aqua-Stop" system is triggered when a leak appears, when water begins to collect in the machine's tank. The hatch is locked, the machine does not respond to pressing the control buttons. The door does not unlock even after restarting. It can also be triggered if the control board is faulty. In most cases, the cause of the fault is damage to the inlet pipe, hose, inlet valve or pressure switch.
F25
The water turbidity sensor, called the aqua sensor, is damaged. The machine does not complete the program, stops and does not respond to pressing the buttons. Occurs when:
- A blockage forms in the drain/water intake system.
- Limescale appears on the temperature sensor.
- Pump failure.
- Dirty water is drawn from the water supply system.
Depending on the cause of the fault, the solution may be:
- Starting an empty wash at a high temperature.
- Descaling the machine parts.
- Installing a filter on the water pipe.
- Replacing the faulty parts.
F26
There is no movement of water due to damage to the electrical circuits of the machine. The cause may also be damage to the pressure sensor. The easiest way to fix it is to disconnect from the network for 20 minutes or reset the programs. If the error does not disappear after restarting the machine, then it is necessary to check the electrical circuits and, if necessary, replace damaged parts. Or service/replace the pressure sensor.
F27
Malfunction of the pressure sensor. It is necessary to check the water pressure. If the specified code is displayed on the machine display, then in most cases the pressure switch - pressure sensor - will need to be replaced. In rare cases, the cause is a software failure on the control board. In this case, the error will be corrected by restarting the machine and disconnecting from the network for 20 minutes.
F28
The flow sensor is damaged. Because of this, water does not fill into the tank of the machine. The error occurs for the following reasons:
- Sensor sensor failure.
- There is no access to water (clogged, pressure is greatly weakened).
- Damage to the control board.
- Solenoid valve failure.
If the water pressure is stable and sufficient for operation, restarting does not solve the problem, then repair or replacement of the failed sensor is necessary.
F29
There is no movement of water through the flow sensor. Occurs in the following cases:
- An error was made when installing the machine.
- Weak water pressure.
- The hatch is not closed.
- There is a blockage in the filter.
- Damaged valve or pressure sensor.
- In rare cases, there is a failure in control.
To fix the problem, you need to check the hatch to make sure there is sufficient water pressure. Check the filter. Make sure the machine is installed correctly. If necessary, repair the valve or pressure switch.
F31
The water level in the tank has been exceeded.The reason may be incorrect installation of the machine, due to which a siphon effect appears. Perhaps only the machine hose is installed incorrectly. The pressure sensor, pump, water intake valve or control system has failed.
To eliminate the malfunction, you should check the correct installation of both the machine completely and the water intake hose. If necessary, replace or repair the pressure switch, pump, valve. Carry out maintenance on the control board.
F34
The hatch does not lock. The reason is a broken lock, sagging of the hatch cover, displacement of the latch. It is also possible that the lock does not close due to laundry, or there is a malfunction in the control board software. If there are no obstacles to closing the hatch, the control system is working properly, and restarting does not eliminate the problem, then repair of the hatch door lock/hinges is necessary.
F36
Damage to the hatch locking device.
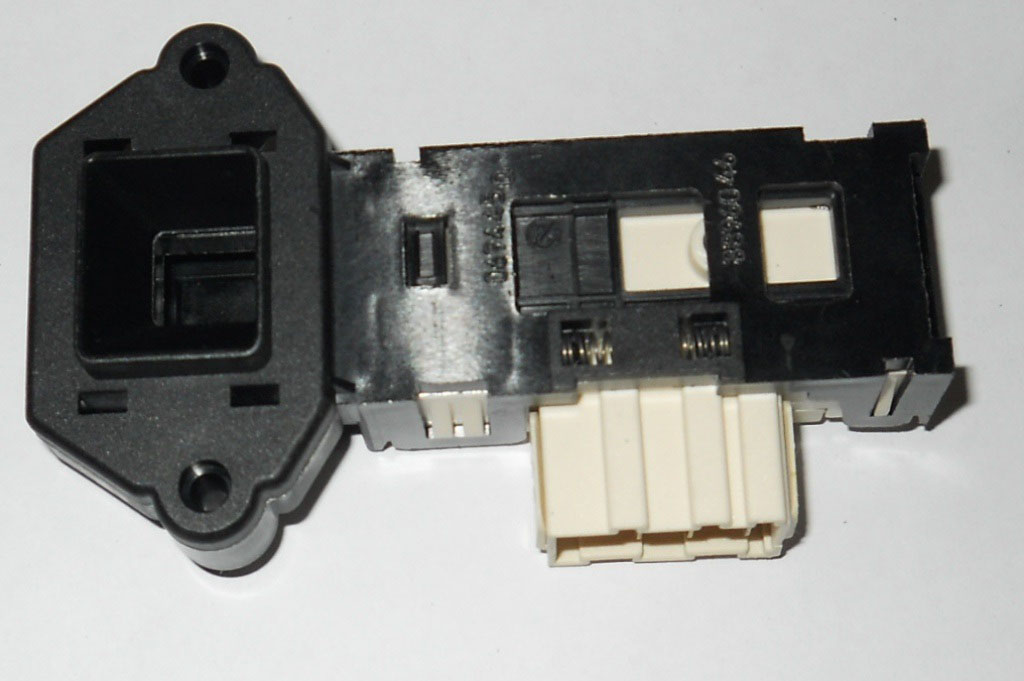
washing machine UBL module
The wash does not start, the specified code is displayed on the screen. If this error occurs, it is necessary to replace the device for blocking the hatch cover.
F37
The temperature sensor is faulty. The machine does not heat the water to the required temperature and stops while the program is running. Both the sensor itself and the wiring leading to it may be faulty. If disconnecting from the power supply for 20 minutes does not eliminate the error, then replacing the sensor or its wiring is necessary.
F38
Short circuit in temperature sensor. Occurs when the system thermistor breaks down, there is no voltage in the electrical network, or there is a malfunction in the control module. To resolve the problem, do one of the following:
- Ensure the required voltage level in the network.
- Service or replace the thermistor.
- Carry out maintenance of the control board or reflash it.
F40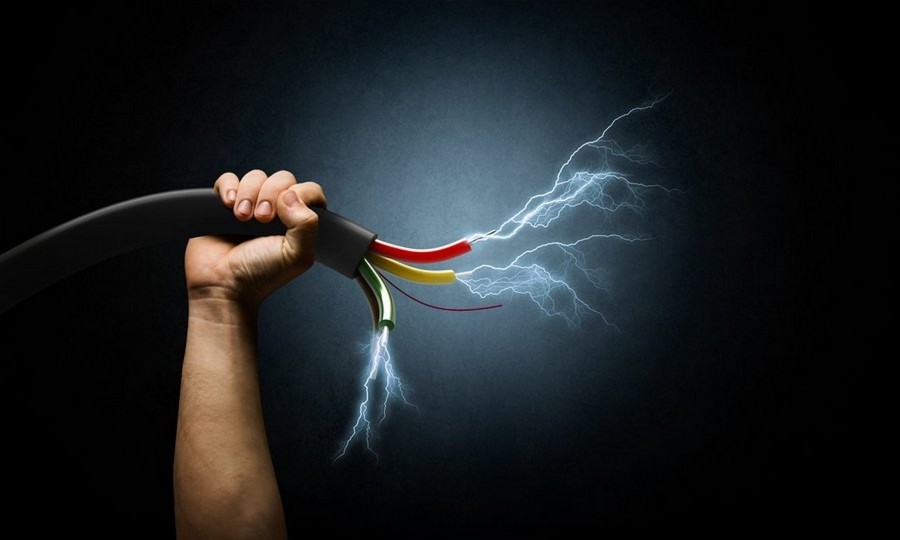
Electrical error. The washing machine does not turn on, the indicators on the control panel do not light up, and there is no response to pressing the control buttons. Occurs in one of the following cases:
- The power supply has gone out.
- The plugs in the room or the machine were knocked out.
- The machine's power cord and plug are damaged.
- The socket to which the machine is connected is faulty.
- The machine's start button is broken.
- The control board software is faulty.
If the wiring in the room is in good working order and functioning, and the machine’s socket is also working, then it is necessary to repair the power cable or control board.
F42
Exceeding the permissible drum rotation speed. The machine works, but vibrates and makes a lot of noise. Reasons for the error:
- Damage to the rotation sensor.
- Machine engine failure.
- Failure in the control system.
The machine must be immediately disconnected from the power supply and wait 20 minutes. If, after restarting, the rotation speed of the drum does not return to normal, then repair of the engine or the rotation sensor of the machine is necessary. The wiring leading from the control board to the sensor or motor may be damaged.
F43
Engine blocking. The machine vibrates a lot. Reasons for the error:
- The machine tank is overloaded with laundry.
- Drum bearings do not rotate.
- The drum speed sensor is broken.
- Failure on the control board.
Remedy:
- Reduce drum load.
- Remove the thing that is blocking its rotation.
- A temporary failure on the board can be resolved by restarting the machine.
- Carry out maintenance on bearings or speed sensor.
- If necessary, replace failed parts.
F44
The machine motor does not rotate in the opposite direction. If an error occurs, the machine stops while the program is running and does not respond to buttons. The display shows the specified error code. Causes:
- The board triac is damaged.
- The reverse relay does not work.
- The tank is overloaded.
- Failure in the control system.
First you need to check the level of loading of the machine tank. If the source of the problem is the control board software, then the error is eliminated by restarting the machine or by flashing the board. In other cases, it is necessary to repair or replace damaged parts.
F59
3D sensor error. The error occurs while the machine is operating. The washing program does not end. The problem occurs for one of the following reasons:
- Board controller failure.
- Weak contact of the sensor cable.
- The sensor itself is damaged.
Ways to resolve the error:
- Restarting the machine.
- Re-flashing the module.
- Reinstallation of loop contacts.
- Replacing a damaged device.
F60
Incorrect value on the flow sensor. When this error appears, the machine does not fill with water. The error occurs when:
- Clogged filter.
- Water pressure too high or low.
- Damage to the flow sensor or the wiring to it.
- Failure in the control system.
- Malfunction of the fill valve or drain pump.
Remedy:
- Restart the machine with a shutdown for 20 minutes.
- Normalization of water pressure.
- Repair/replace damaged sensor, wiring, board, valve or pump.
F61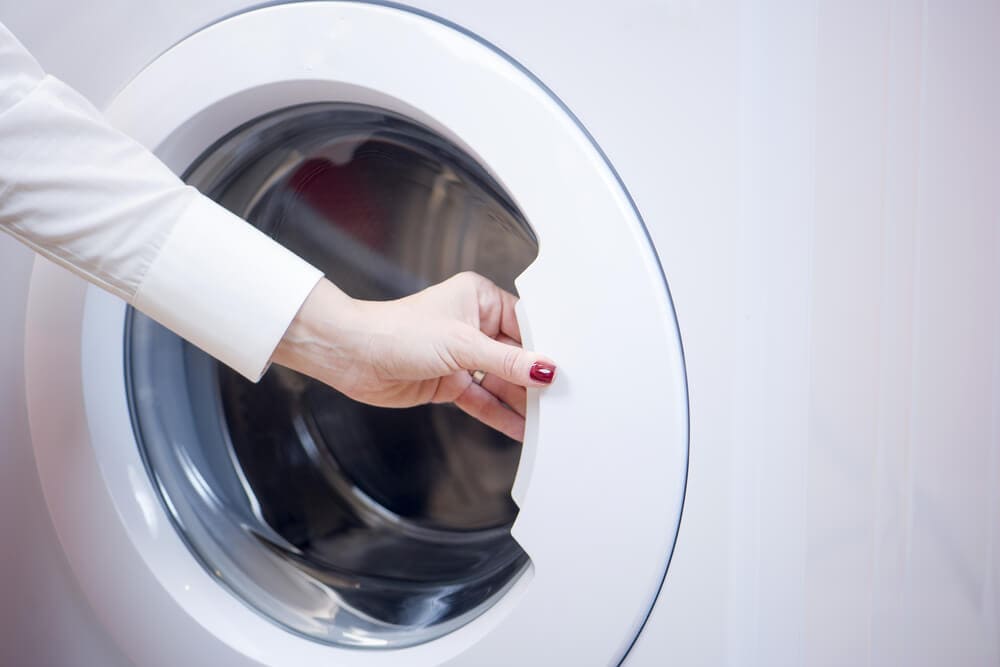
Sunroof error, incorrect code. Occurs when the tank door of the machine does not close. The causes of error F61 are:
- Damage to the locking device.
- Damage to the wiring to the device.
- Control module error.
To resolve the problem, do one of the following:
- Disconnect the machine from the power supply for 20 minutes.
- Reset the running program with the corresponding control button.
- Replace damaged wiring.
- Repair or replace the locking device and control module.
F63
The security program has triggered. The protection is triggered when a failure occurs in the control module software or the control chip breaks down. The error can be resolved by rebooting the machine (disconnecting from the power supply for 20 minutes and turning it on again).
It is necessary to diagnose the entire control system. If damage is detected on the control board or chip, the control devices are repaired or replaced. In this case, diagnostics should not be neglected, even if the machine started working after restarting.
F67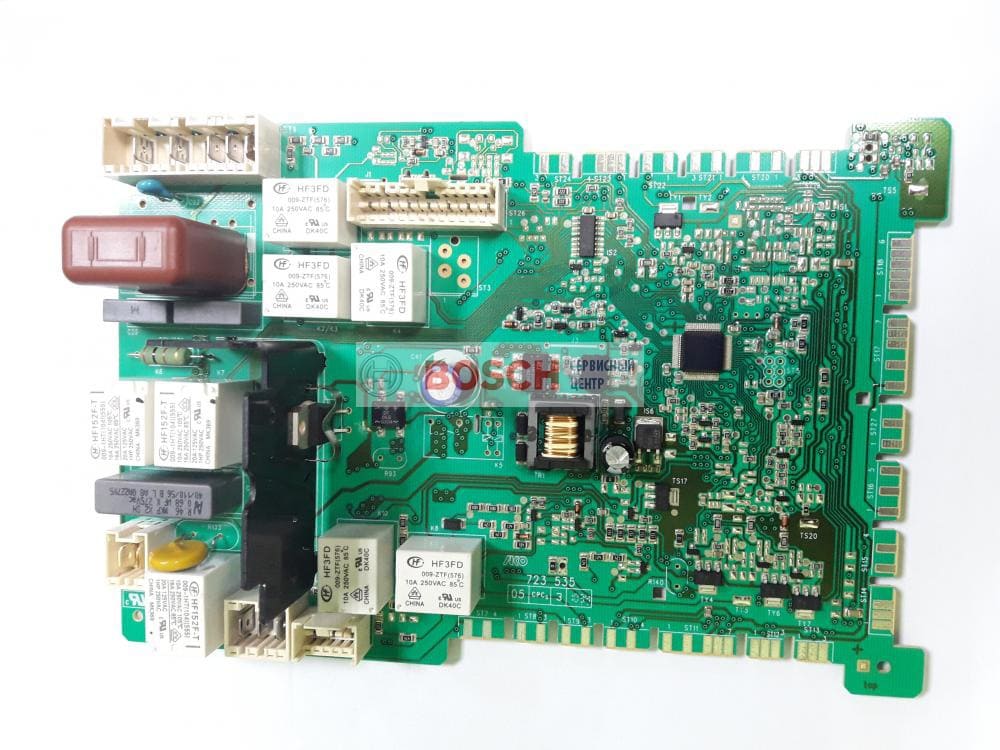
The control board controller is damaged. When this error occurs, the machine does not turn on and does not respond to pressing the control buttons. Can be eliminated by restarting the machine (disconnecting from the network for 20 minutes and turning it on again).
If restarting does not help, it is necessary to conduct a full diagnosis of the control board and, if necessary, repair it or replace it with a working part. As a rule, repairs are possible if the control board chip is working properly.
Conclusion
In most cases, errors can be corrected by rebooting the machine or fixing water/electrical problems. You can do this yourself or call a plumber to fix water problems or an electrician to normalize the network. A common cause of many errors is incorrect installation of the machine.
Knowing the error codes or similar indicators on non-display models of washing machines will allow you to quickly determine the cause of the malfunction and begin to eliminate it. If repairs or replacement of parts are necessary, you should contact a washing machine repair specialist. The installation of the machine should also be entrusted to an experienced technician. similar entries from this section