Experienced craftsmen who repair laundry washing machines rarely encounter models from this company. In the Russian markets, in comparison with Indesit, Samsung and other well-known brands, such a brand is quite rare. Repair of Asko washing machines, as well as the failures of such devices themselves, are particularly specific. This is exactly what we will be talking about today.
Basic malfunctions of Asko washing machines
Although such machines are much less common than others, failures in them occur with the same consistency. Owners of such devices turn to service centers for help with the same problems:
- the drum rotates too slowly, the tank does not rotate at all;
- it is impossible to close the hatch, or it is completely blocked;
- laundry is washed in cold water even if high temperature conditions are specified;
- The washing machine does not drain waste water, the program freezes.
Naturally, other breakdowns also occur, but they happen much less frequently or are considered typical with machines from other companies.
Considering the washing mashines of our brand, it is necessary to note that ASKO is distinguished by certain oddities. According to reliable sources, in Finland, a quarter of the residents buy just such machines and are satisfied with their operation.But in Russia and other CIS countries, such machines constantly break down. And there are plenty of reasons for this - the quality of assembly work, hard tap water, poor washing powder. There are also problems due to violation of operating rules, which are defined in detail in the operating instructions for the device.
Asko washing machine repair
Not in every case you can do the repair work yourself, because the machine has complex electronics. But there are situations when this is quite possible if you follow the instructions below.
- The drum does not rotate.
Most often, repair of Asko washing machines is necessary in cases where the electric motor does not rotate the drum with things well enough or simply refuses to perform this function. It would be easier to understand the problem and repair the washing machine yourself if the self-diagnosis system worked constantly. But in reality it turns out that the drum does not rotate, but error code is not highlighted. What could be the reason? Most often, this problem occurs due to the drive belt. It does not jump off, but slips along the pulley and does not create normal rotation. It turns out that the drum is under load, or is simply idle or spins slowly, producing from one hundred to one and a half hundred revolutions in one minute. But this speed is extremely low not only for spinning, but also for washing with rinsing.
If we look deeper into the problem, the cause may not be in the belt itself, but in the motor pulley. Perhaps it was installed poorly at the factory, or it was damaged during operation, but the fact is clear! So the pulley will have to be changed, proceeding as follows:
- The back panel is removed from the machine;
- We pull the drive belt off the pulley and inspect it;
- if damage is detected on the pulley, then it is necessary to disconnect all the wires and unscrew the electric motor;
- you need to take a bearing puller and a blowtorch and go outside, since it is not recommended to perform such work indoors;
- A puller is installed on the pulley and tension is created. You should not immediately tear off the pulley, as you can break the puller;
- Now you should light the lamp, warm it up and begin to carefully heat the pulley with a flame. In this case, it is necessary to ensure that other metal elements do not heat up;
- the heated pulley should be dismantled almost independently;
- now you need to cool it down and purchase exactly the same element in the store;
- the new analogue is also installed in a hot state, heated to red with a lamp;
- as soon as the new pulley is in place, it should be cooled, the engine and drive belt should be installed, which is also changed first;
- The panel is installed, the machine is connected and tested.
It must be remembered that if the machine produces error code E 01, then the problem must be looked for in the electric motor itself or in the board responsible for the control. It is recommended to entrust such work to an experienced specialist.
- The door does not lock.
This problem occurs quite often - the drum does not lock. It all starts with the fact that the locking mechanism on the hatch stops working normally, and the machine “freezes” during startup. As a rule, an experienced housewife finds a way out of the situation - she presses the door with her knee and restarts the machine, which washes in normal mode for some time.But after a couple of years, the mechanism completely fails, and the washing machine does not turn on.
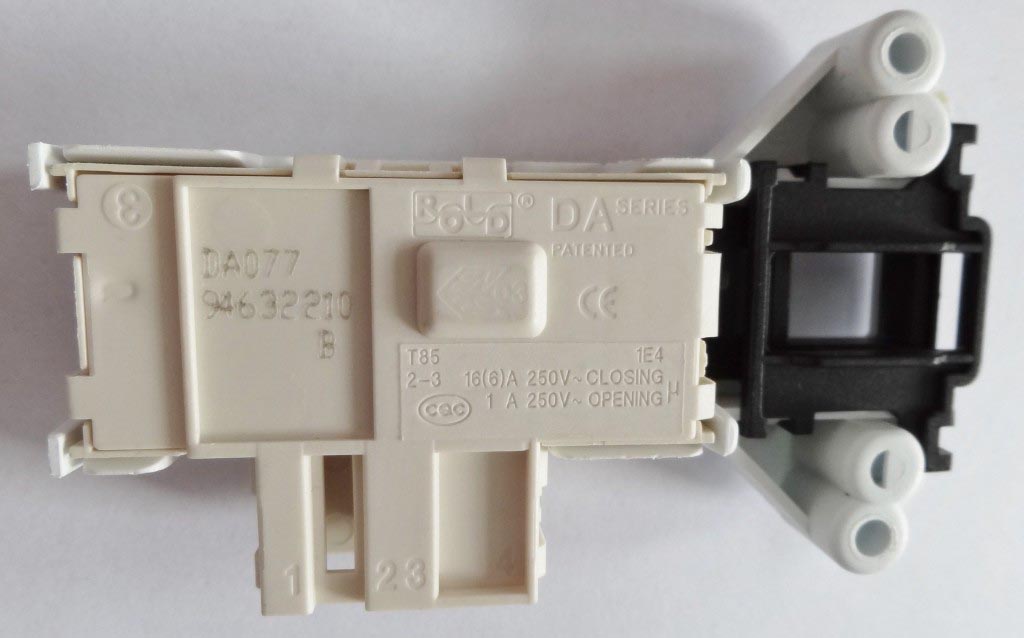
Hatch locking device
In this case, various kinds of pushing no longer help; you will have to disassemble the mechanism responsible for closing the hatch and replace the locking device.
- The washing process takes place in cold water.
Such refusal also happens, but a little less often. And in most cases, the situation can be corrected quite quickly, since when a problem occurs, self-diagnosis is triggered, and errors with codes E 05 or E 06 are displayed on the screen. What may be the reason:
- temperature sensor failed;
- there is no contact from the control module to the temperature sensor;
- The board's triac, which is responsible for the heating element, has lost its functionality;
- The water heating element has failed.
What exactly happened remains to be seen. You need to start by diagnosing the heating element and temperature sensor. But first you have to get to them.
Here you should know that in many models both elements are located either in front or behind the tank. But in our case, the heating element is located on the side. The placement is not quite ordinary, and you need to know how to act in this case. There is nothing complicated here - we remove the back panel, remove the drive belt, and the contacts of the heating device open in front of us.
Further:
- We will check using a multimeter set to minimum;
- disconnect all wiring from the heating element and temperature sensor;
- checking contacts. If the device shows a resistance of about 28 Ohms (the power of the heating element is 2 kW), then everything is in order;
- All that remains is to “ring” the temperature sensor. First, disconnect the drain pipe and remove any remaining water;
- remove the sensor;
- pour warm water into the container and immerse the element being tested into it;
- We take it out after a couple of minutes, set the multimeter to minimum, and lean the probes against the contacts. If 40 - 60 Ohms are displayed, then everything is fine - the element is working.
Now all that remains is to check the wiring leading from the heating element and sensor to the control module, ringing them in turn. If everything is in order, then the problem may be hidden in the module itself. In this case, you should not take independent action - contact an experienced specialist.
- Waste water is not drained.
When the machine stops draining dirty water and stops the washing program, but the floor is dry, then it is more likely that one of the following faults has occurred:
- clogged pipes or drain hose;
- the pump failed;
- the sensor indicating the liquid level has failed;
- there is a break between the control board and the pump, or between the board and the sensor indicating the level.
Before looking for the cause of the problem in the electronics and electrical wiring, it is necessary to perform a general cleaning of the machine. This will require some effort, but after such measures the drainage can resume and the machine will start working normally again. But if this measure does not help, you will have to take a multimeter and call the pump, water sensor, and electrics one by one, looking for breakdowns. First the pump is checked. The resistance on it should be about 144 Ohms, then it’s the turn of the sensor, the value of which should be 60 Ohms. At the very end it is the turn of the wiring. If a break is not detected, then the problem lies in the microcircuit, and you need to seek help from a specialist.
Basic error codes
The electronics of the ASKO machine are designed in such a way that it is able to display codes indicating certain failures and malfunctions. The number of flashes in each series determines the code. Understanding what it means, you can repair the unit yourself without contacting the service department.
You should not panic if the unit display shows letters and numbers instead of the time during which the machine should complete the process. As a rule, this happens at the moment when the module responsible for controlling the process detects a failure of some node. We can confidently say that all breakdowns caused by a failure of the control unit occur in twenty percent of situations; all other problems occur in the water heating element, pressure switch, electric motor, drainage system and inlet valve.
To identify a part that has failed, the machine has a self-diagnosis function that displays an error on the screen. First you need to check the presence of voltage in the network, the functionality of extension cords and tees. They may not provide normal voltage and can cause serious problems. check the drainage system, as it most often fails in every household appliance for washing clothes.
The reasons for the occurrence of error codes and their interpretation are given in the table:
Code | Reason for appearance | Inspection and repair |
E 01 | Drive motor failure | Failure of one of the elements of the engine power supply system - the control triac, reverse relay, connecting elements, the engine itself. In addition, in this case it is recommended to check the tachogenerator. If all elements are in good condition, the controller should be completely replaced. |
E 02 | Problems with water filling.An error is displayed when the tank is not filled to the required level. | The defect may be caused by:
– lack of water in the water supply system; – damage to the intake valve; – clogging of the intake hose; – malfunction of the electrical controller; – failure of the sensor indicating the water level. |
E 03 | Waste water does not drain | You should check the reliability of the connection between the controller and the water drain pump. The voltage is checked at the pump contacts. If the result is negative, the pump itself, the weight of its connection and the electronic controller are checked under voltage.
Then the water level sensor and its connection to the board are checked. It is also necessary to inspect the water drainage channel for clogged areas. If everything is in order, then you will have to replace the electrical controller. |
E 04 | The tank does not fill with water after a certain time | There may be insufficient water pressure in the water pipe.
There are blockages in the valve, filter or pipes. |
E 05 | The water temperature is higher than set by the program | In this case, it is recommended to check the temperature sensor, water heating element and all wiring connected to them. If everything is in order, then the controller is replaced. |
E 06 | The water has not warmed up to the temperature set at startup. | It is necessary to check the heating element and its wiring, and replace the controller if necessary. |
Door lock fault | The machine door did not close tightly | Typically, to reset the error code, you must close the sunroof again. If the code does not disappear, you should check the locking device and the electrical controller. |
Floaming | There is too much foam | If this error occurs, you must activate the “Rinse” function.In the future, it is necessary to use other detergents, observing the norm of their laying. |
Over flow | There is more water in the tank than the level | It is necessary to check the inlet valve, the sensor showing the level and the controller itself. When the water level has approached the desired mark, and the drain pump has not worked, it is necessary to check it too. |
Termistor fault | The temperature sensor has failed | The element should be checked for an open or short circuit. |
Pressure sensor error | Failure of the level sensor | The sensor and its pipe, which is connected to the tank of the washing machine, are inspected. |
Conclusion
It should be noted that if you became the owner of an ASKO washing machine assembled in Finland or Sweden, then you are very lucky. New equipment will work for you for at least two decades. And if before that it worked for ten years in Europe, then it will serve you for fifteen years.
Once again, I would like to draw attention to some points. A large number of failures can be eliminated on your own, if you carefully study all the operating instructions and the information provided above. But when a problematic issue with the electrics arises, it is better not to take independent action, but to call an experienced specialist. He will be able to check and carry out repairs, giving a guarantee for the subsequent operation of the unit. Do not take risks, since the repair will cost you a tidy sum in the future.
Hello, I have an asko w8844 xl w washing machine, please tell me where the fuse is located in this model.
1. Inside the plug from the wire connecting to the network.
2. At the end of the network connection wire, which is located inside the housing.
3. On or near the electronic board.