A washing machine is a faithful assistant in any family. It’s unpleasant when it breaks and you have to wash a bunch of laundry by hand. Breakdowns of such large equipment as a washing machine almost always lead to calling a technician and unnecessary expenses.
Minor faults of washing machines can be fixed at home, but to get rid of large ones you will need qualified assistance from a specialist. Next, we’ll tell you how to independently assess the extent of the damage and fix some simple washing mashine breakdowns using home methods.
Determining the malfunction of washing equipment by codes
All washing machines can be divided into two categories - with electronic or mechanical control.It is the first type of washing machine - with electronic control units - that is capable of diagnosing operational deficiencies and displaying a breakdown or damage code on a special display. Using this code and the instructions for the machine, anyone can determine what happened to the unit and how to fix the problem.
You need to understand that each manufacturer has its own coding of faults, so it is best to refer to the instructions at the slightest suspicion of improper operation of the unit.
Modern washing machines are very sensitive to operating conditions, so they often issue fault codes that are easy to fix: a clogged filter, a loose door, a problem with water intake, or simply a lack of electricity in the network.
Washing equipment does not turn on
Sometimes a deadlock situation arises when the laundry and powder are loaded, but the machine not only refuses to work, but does not even want to turn on. There is no need to panic or get upset. The unit may not start working for several reasons:
- there is no voltage in the electrical outlet - you can use a multimeter or any working household appliance to understand whether there is really no current;
- there is damage to the plug - you need to check its integrity and contacts;
- the child protection function is active - look at the display, if there is a “lock”, then you need to disable this option, which blocks the start of washing;
- the loading hatch is not tightly closed - either you did not close the door yourself, or for some reason the lock did not work correctly, you can open and close the hatch again;
- failure of the electronic control unit - this will become a problem, since repairs are performed only by a qualified technician, and replacing the electronic control module is expensive.
If you cannot determine why the machine does not turn on, then most likely the problem is a malfunction of the control module, and you should call a technician.
There is no water flowing into the washing machine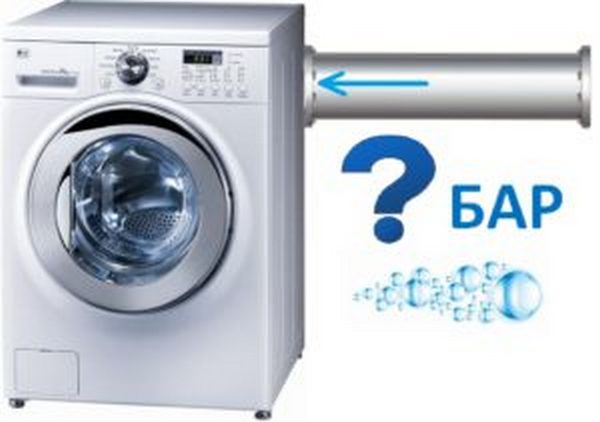
This problem can be expressed in different ways: water is not collected into the tank at all or very little is collected, water may quickly drain when filled or may not fill the compartment with powder. Each case has its own reasons, we will tell you about them in more detail:
- If water does not flow into the tank at all, it means that the solenoid valve is damaged or broken. The instructions should describe the location of this machine element and how to replace it. This can be done at home if you have a little skill in working with such devices.
- When water is collected very poorly, it means that the water level sensor is malfunctioning. We disconnect the pressure hose and blow it with air, and normally there should be sounds similar to clicks. If they are not there, then the sensor is faulty and needs to be replaced with a new one.
- If the water drains after filling, it means that two hoses are installed incorrectly: water supply and drainage. Check them out.
- Does water not fill into the detergent and powder compartment? This means that the filter in the water supply hose is clogged and needs to be removed and cleaned. Also, the reason may be due to weak water pressure, so the powder will not dissolve completely and will clog the hose.
- The washing mashine door locking device or electronic control unit may also malfunction. It is better to entrust the repair of these machine elements to a specialist.
After you have fixed the problem of water intake, turn on the machine for one wash cycle without laundry. If everything is in order, then you can wash your things.
Washing machine door won't open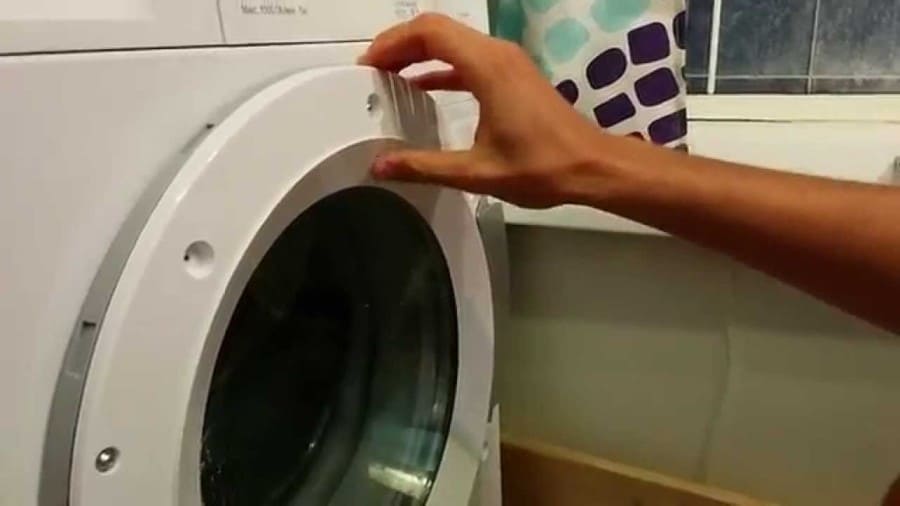
A fairly common problem faced by users of conventional washing machines is when the wash is completed and the loading hatch does not open. In such a situation, many people call a professional, and the laundry is washed additionally so that it does not become damp.
There are two main reasons why the door does not open after washing:
- the water is not drained completely, or the water level sensor is broken;
- door lock device is broken.
If the water does not drain completely after washing, then the problem lies in the following elements of the machine: filter, pump, valves or drain hose.
When the automatic drain does not work, you can drain the water in several ways. For example, using a special emergency hose, through a drain filter or drain pipe. The easiest way is to disconnect the drain hose from the back wall of the machine and pull it out of the sewer, then lower it below the level of the washing machine tank along its entire length and lower the end of the hose into a previously prepared container. However, this method does not work on all washing units. After draining the water, you need to check and clean both the drain hose and the filter, which may be clogged with small objects and accumulated debris. If the filter itself cannot be unscrewed due to scale or small objects, then it is better to remove the front wall of the machine and get to it from the inside.
When a door jams, it is most likely a jammed lock, in which case you can try to open it by hooking the lock hook with a thin line from the outside or inside of the washing mashine. If the mechanism is worn out, it is better to replace it, otherwise the locking problem will be permanent.
The water does not heat up when washing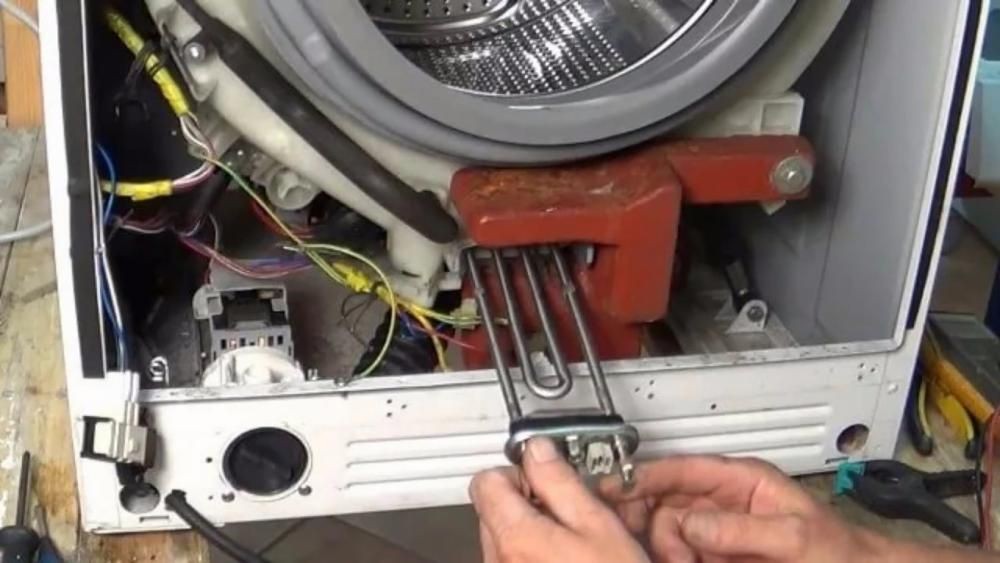
The main reason that the water does not heat up during washing is a breakdown of the heating element or heating element. It may break if tap water contains a lot of magnesium and calcium salts. At the same time, heating elements in inexpensive washing mashine models do not have a protective coating, which accelerates breakdowns due to scale formation.
To understand that the heating element is broken, you need to start the machine in a mode with a high washing temperature, for example, 800C, and after 15 minutes touch the glass hatch with your hand. If it is cold, then the machine is not really heating the water.
Since the heating element cannot be repaired, but only replaced, this procedure is easy to carry out at home, even without calling a specialist. To do this, you need to turn the washing unit on its side and remove the old heating element, disconnecting the contacts and the clamping nut. Next, install a new one.
It happens that the heating element is working properly, but the machine still does not heat the water. There are two reasons for this:
- The temperature control sensor is broken and needs to be replaced;
- There are problems in the electronic control module, and you can’t do it without a technician.
By the way, it happens that the machine heats the water slowly, despite the fact that the heating element is working properly. This may indicate low voltage in the network. Because of this, the washing time of the laundry increases, regardless of which program you choose.
The drum has stopped spinning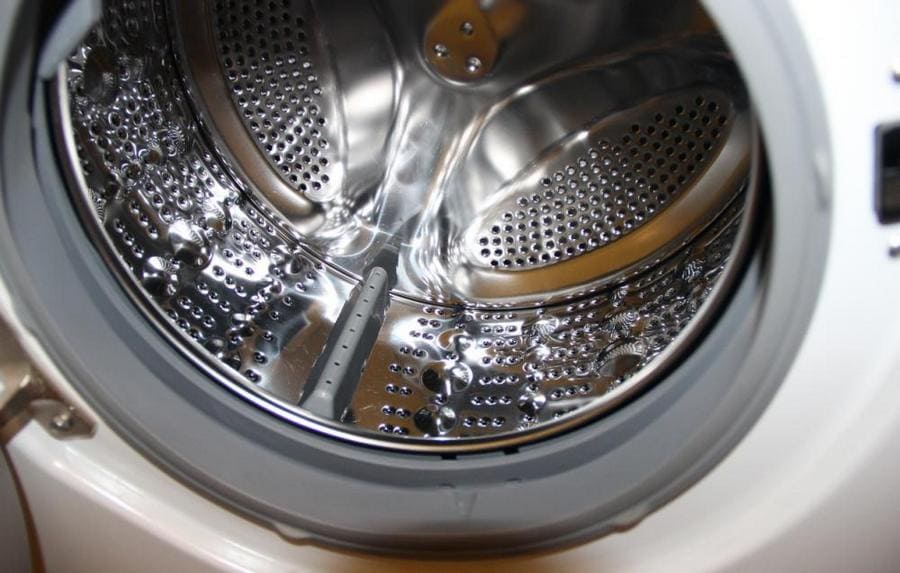
The reasons for this malfunction may be:
- damage to the drum drive belt;
- failure of the electronic control unit;
- problem with the electric motor;
- a large object has fallen into the tank and it interferes with the movement of the drum;
- drum bearing deformation:
- malfunctions in the motor tachogenerator.
It happens that the drive belt falls off and just needs to be returned to its original place.If the belt breaks, it can be easily replaced if you have the right tools at home. When buying a replacement belt, always look at the number of wedges and length - these indicators are different for all machine models.
The brushes in the electric motor often wear out, which you can also purchase and replace yourself.
The washing machine does not spin clothes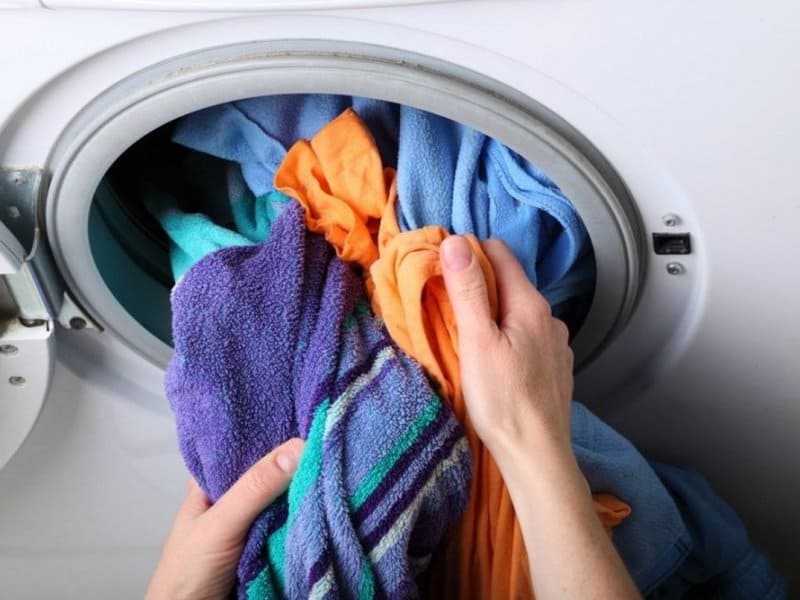
The most common cause of this problem is improper loading of the drum. You either put an item that is too large and heavy for washing, or the amount of laundry by weight exceeds the norm established for this machine model. In this case, it is better to divide the laundry into two parts and wash it separately. You can also manually stir the laundry in the tub and it will wring out more easily.
The washing machine may not drain water if the drain system is faulty and the problem lies in one of these elements: the drain filter, pump, hose or valve.
If the spin cycle is very weak, there may be two reasons:
- The spin mode is incorrectly selected - just move the regulator to the desired position;
- The spin regulator itself is faulty - disassemble the mechanism and see what needs to be repaired or replaced.
Strong noise and vibration during operation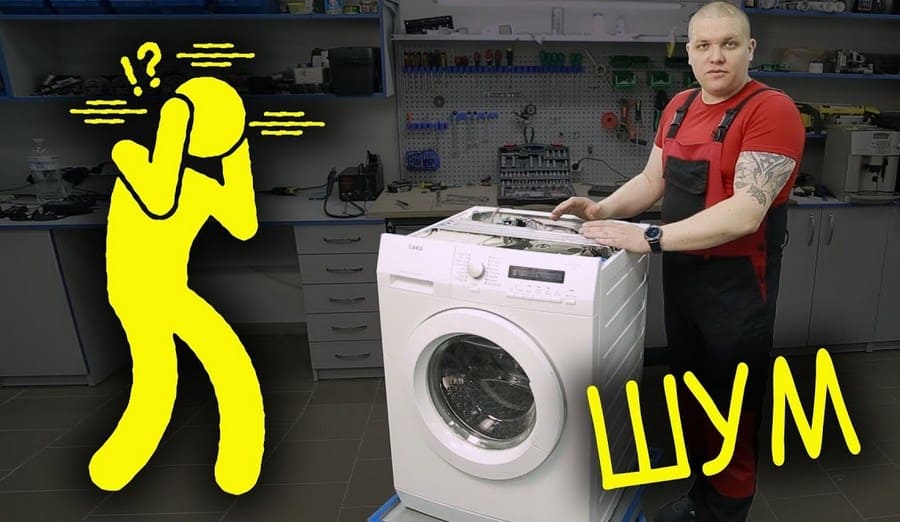
Any washing machine makes noise during operation and vibrates when spinning. However, there are specific noises that indicate that the unit is faulty.
For example, a buzzing sound is a sign that there is a problem with the door locking device. Grinding and crackling sounds indicate wear on the drum bearings. A sharp sound, similar to a squeal, indicates a breakdown of the drive belt.
The causes of breakdowns can be different:
- If foreign objects get into the tank under the drum, for example, large buttons, bra wires, small parts from children's toys, then you will have to remove the heating element and remove the objects so that they do not interfere with the operation of the unit.
- Bearings are worn and damaged. To replace them, you need to understand the structure of the machine, but it’s easier to call a specialist, and he will replace the bearings quickly and efficiently.
- When noise occurs when water is drained, it means there is a problem with the drain pump. First you need to disassemble and clean it. If this does not help, it means that the pump elements are worn out and need to be replaced. It's easier to buy a new pump and install it following the instructions.
- When, during intensive washing or spinning modes, the machine literally jumps and vibrates strongly, it means that it needs to be installed correctly. This is done using a building level. To prevent the washing unit from moving during washing, you can use silicone pads.
It is also better to once again check the thoroughness of the drum fastenings and counterweights. Make sure there is no play on the bearings.
Linen and things have an unpleasant odor after washing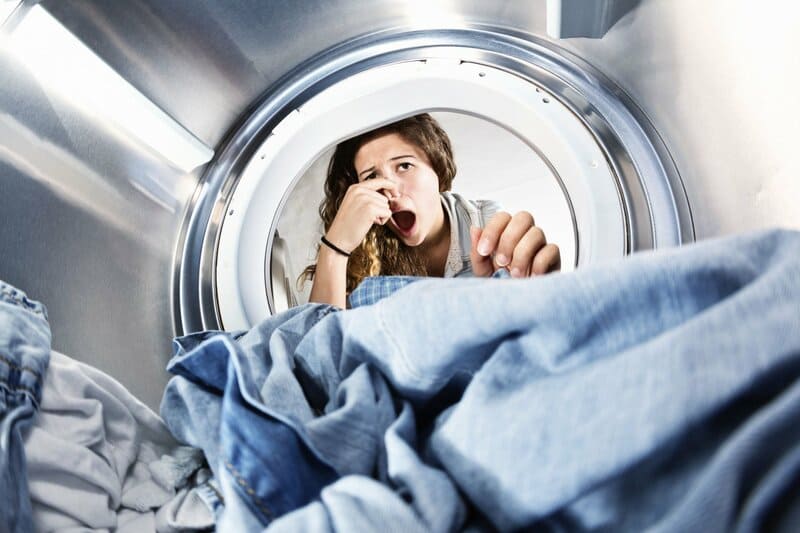
If, when loading or unloading laundry, the machine and the clothes themselves emit an unpleasant, rotten smell, then there is a problem with the cleanliness of the unit. Most likely, dirt has accumulated in large components, filters, hoses and behind the hatch cuff, and even mold has appeared. How to deal with this?
The easiest way is to wipe the tank and rubber door seals with a dry cloth after each wash, and also leave the machine open for about an hour, or leave it open when the laundry is not washed. During this time, it will dry out and mold will not form in it.
If mold appears, then you need to start washing without laundry, but with citric acid and any disinfectant. The inside of the washing mashine will be washed, citric acid will remove lime deposits, and a disinfectant will destroy bacteria along with the odor. This cleaning should be done at least once a month.
Also, visible mold stains can be wiped off with a sponge soaked in chlorine disinfectant before idling.
Another reason for the odor problem may be improper installation of the drain hose - it is installed below the level of the drum, in which case the smell from the sewer enters the machine and the laundry also deteriorates. Fix the hose higher, install a check valve, and rinse and dry the washing mashine. The unpleasant smell will go away.
Some machines have special high-temperature cleaning modes where all germs are killed by heat.
The washing machine is leaking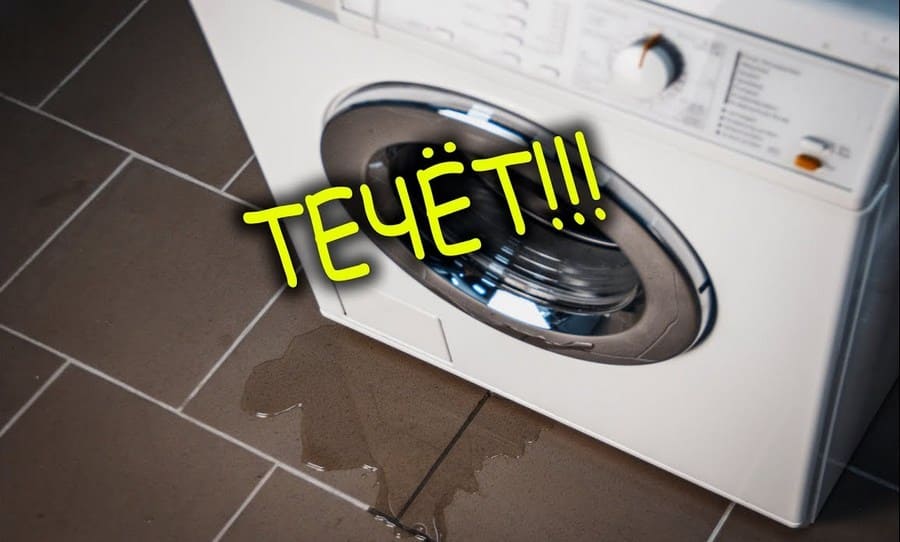
If a puddle of water accumulates near the machine when washing, it means there is a problem in these units of the device:
- wear of the water supply hose;
- the door seal is leaking;
- problem with the filter and pump;
- the tank seal has leaked;
- The powder dispenser or associated hoses are leaking.
What you can do yourself to fix leaks:
- check the drain hose and tighten the nuts or replace it if worn;
- thoroughly rinse the powder dispenser and remove any blockages;
- slightly reduce the pressure of the water supplied to the machine.
If you were unable to fix the leakage problem yourself, then call a technician.
The control unit of the washing equipment is broken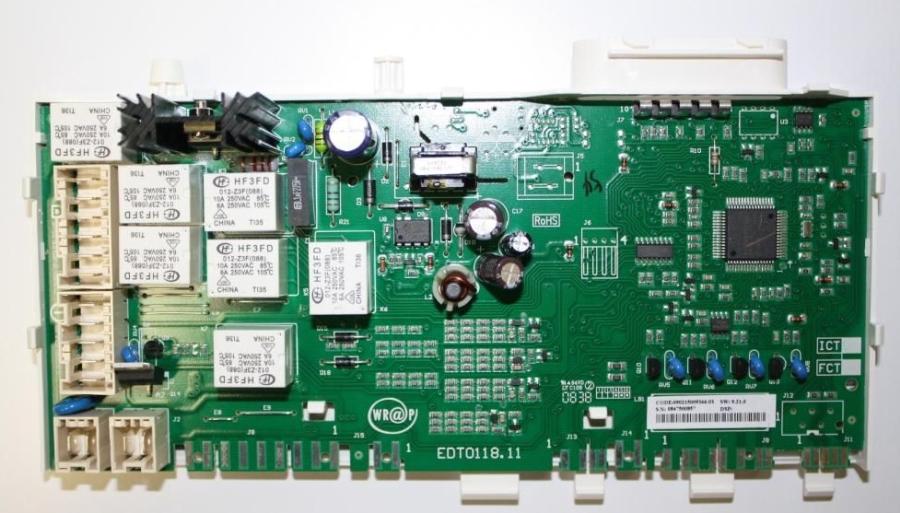
The electronic control module is a complex device, and it will not be possible to repair it yourself without the necessary knowledge and skills.It should be noted that replacing it will be very expensive, and if the machine is cheap, then it is better to generally buy a new and reliable unit.
There are many reasons why the control unit fails:
- during an internal leak, water flooded the ECU contacts or boards, causing a short circuit;
- perhaps the triacs that control the operation of the heating element, electric motor, pump and other important components of the machine have deteriorated;
- problems with ECU chips;
- breakdown of the network filter capacitor;
- due to increased vibration, the contacts of the cable connectors are broken.
In any case, if you suspect problems with the ECU, it is better to immediately call a technician, who will definitely sort everything out and repair the washing unit.
The washing unit is electrocuted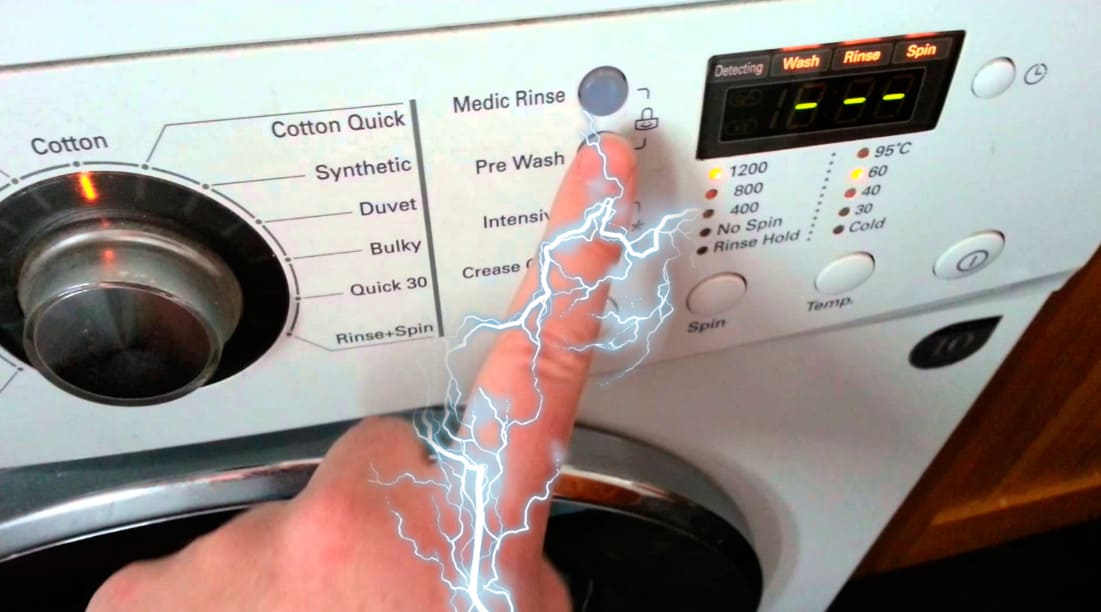
Since any washing machine is an electrical appliance, it means, theoretically, it can pass current to the body. This usually happens if there is no grounding.
There are two ways to solve this problem:
- installation of RCD;
- make grounding in an apartment or house.
A residual current device (RCD) cannot completely eliminate electricity leaks; it will only reduce its intensity. Therefore, only properly performed grounding can save people from accidental electric shocks.
If current gets to the drum - this is felt when loading or unloading laundry, then one of these malfunctions is present:
- breakdown of the heating element or motor;
- there is an insulation violation;
- The socket to which the washing unit is connected is faulty.
In order for the washing machine to serve faithfully and not give an electric shock, it is better to follow a few simple rules:
- Do not install the device in a room with high humidity;
- do not plug in the machine with wet hands;
- First you need to load the laundry for washing and only then turn on the unit;
- After completing the wash, unplug the machine and remove the items.
If when you turn on the machine there is a burning smell, it means that the wiring in the machine has shorted. It urgently needs to be disconnected from the network and a technician is called.
Typical breakdowns of washing machines from different manufacturers
Manufacturers of different models of machines always try to make their products not only affordable, but also easy to use. Sometimes innovations turn into design flaws, and each brand has its own weaknesses. Let's tell you more about them.
Ardo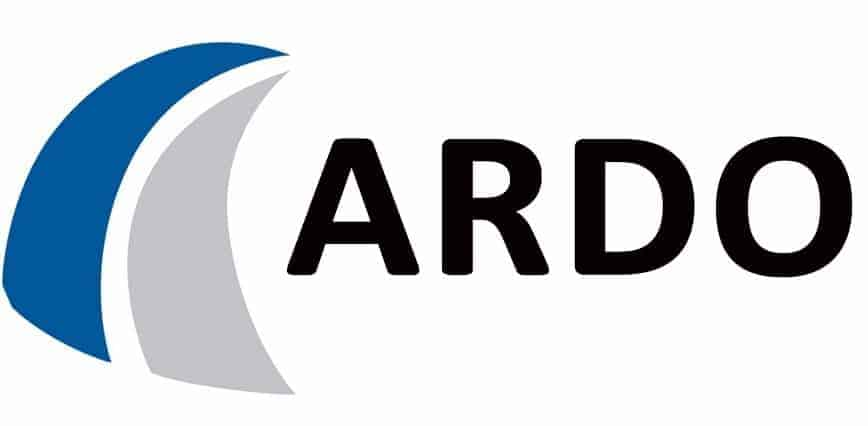
In inexpensive Ardo washing machines, increased vibration causes the control module to shift. The heating element often fails, or leaks appear due to unreliable gaskets. In models with vertical loading, after 3-4 years of operation, rust appears on the top cover of the drum. Narrow Ardo machines sometimes make a lot of noise when operating at high speeds. Repair of these popular washing mashines is inexpensive, so despite the breakdowns, they are loved by customers.
LG
Popular washing machines in LG lines are with direct drive. In this design there is no belt drive. This significantly increases the service life of the machine and the reliability of its operation.
But LG machines have a problem with the water drainage device. The filter and path become clogged more often, which causes errors and operational failures. By the way, the code for this error is specifically written in the instructions so that the owner of the unit can clean the drain in time.
There are also difficulties with the valve and water supply sensor. This is where rubber seals made of soft material suffer and wear out. The sensor often jams and too much water is collected.At the same time, the water begins to drain because the tank is full.
Indesit
This brand produces some of the most budget-friendly washing units. Cheapness turns into an unpleasant side - heating elements are made without a special coating and quickly fail under the influence of hard tap water. Such machines operate for no more than 4-5 years.
There are also problems in the operation of washing programs and modes: programs often freeze, are not executed completely, and the machine eventually breaks down. This indicates a poor quality performance of the electronic control module. It constantly requires attention and minor repairs. Replacing it is expensive. Therefore, if you need a washing machine for a large family with frequent washes, then Indesit is not the best choice.
Bosch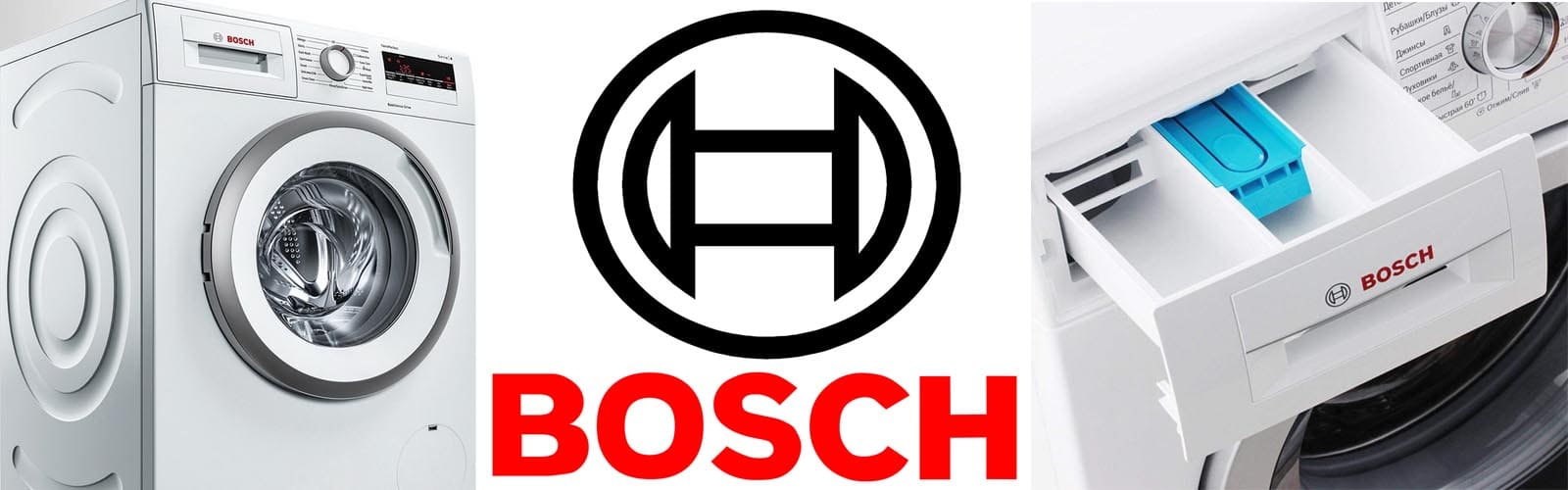
Bosch produces the most reliable washing machines in the mid-market segment. These units are distinguished by their quality of workmanship and attractive design. Bosch machines do not often require repairs if used carefully.
However, these machines also break down. Most often, problems arise with water sensor controllers or a filter clogged with dirt. These difficulties can be easily resolved at home with the help of instructions.
Ariston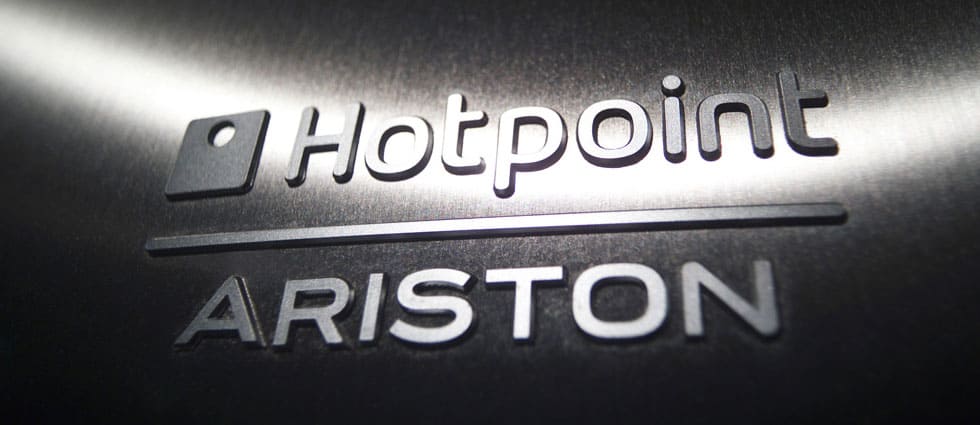
The machines from the American manufacturer are reliable and easy to use. But they can also break, especially if operating conditions are not met. These machines do not tolerate hard water or untimely cleaning.
Some models have a problem with a specific odor from the rubber seal on the hatch. Moreover, even over time it does not disappear.
There is also a design feature - strong vibration when spinning or operating at high speeds. This leads to damage to the ECU and requires contacting a technician.
Samsung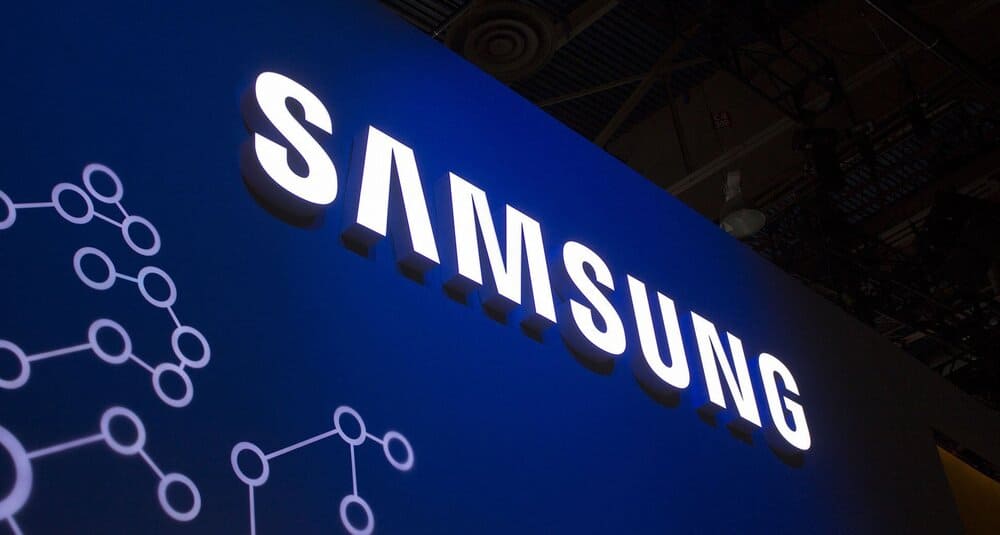
One of the most popular washing machines on the market.Overall, they are well-built and quite reliable. According to statistics from services, the control module in Samsung machines breaks down extremely rarely, which indicates a high build quality.
But there is a problem with the heating element, which quite often deteriorates from hard water and fails. True, the heating element is easy to replace without the involvement of a specialist.
Some Samsung models can vibrate strongly and make increased noise when operating at high speeds. Under such conditions, the belt often breaks and has to be replaced. Here it is important to choose the appropriate model in length.
Samsung bearings are of very high quality and rarely break.
The filter on the water drain is located very inconveniently, so users are often too lazy to clean it. Because of this, the drain becomes clogged.
There is also a design flaw in the form of a too short water drain hose. Because of this, valves may malfunction due to water hammer, and water will flow back into the machine.
Electrolux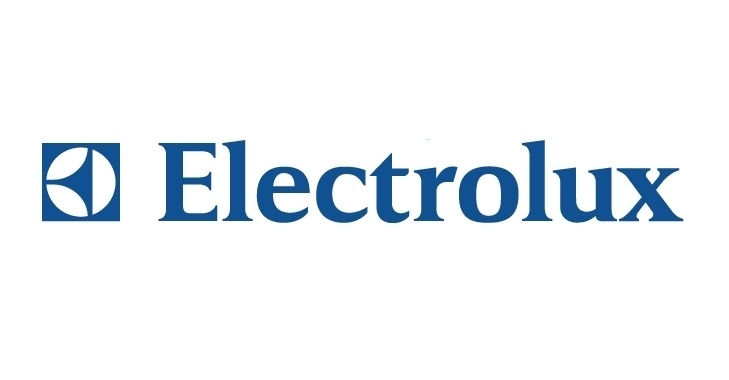
The power button and power cable on these machines are often poorly made, which can cause them to fail. Over time, the cable becomes frayed and the contacts are broken. In this case, you will have to check the entire cable to find the leak.
There are malfunctions in the operation of the control module: programs fail and washing modes are not followed. In this case, it is better to contact a service center to reflash the ECU.
Prevention of breakdowns
If you treat your washing machine with care and follow all care instructions, then frequent repairs will not be required.
According to reviews from service technicians, washing mashine owners often turn to them with problems that arise precisely because of improper operation of the units.
To make your washing machine last longer and break down less, try to follow these simple rules:
- When transporting the machine, protect it from shock and moisture;
- installation of the machine must be done using a level and silicone pads;
- Do not load a lot of laundry in one wash cycle;
- use special powders with reduced foaming and do not overuse anti-scale compounds;
- If the water in your region is hard, it is better to wash at temperatures up to 700WITH;
- regularly clean all filters and dry the machine after each wash;
- If it seems to you that you hear suspicious noises when the machine is operating, then it is better to immediately find out what is wrong so that the machine does not break down.
Thus, most breakdowns can be avoided if you treat the washing machine with care and follow all operating and maintenance rules. Minor repairs can be done at home by replacing some parts yourself. To do this, purchase only branded spare parts that strictly match the model of your washing machine. In case of major breakdowns, it is better to contact a service center.