The motor is the most important part in any washing machine. In order for it to work properly and have optimal settings, it is necessary to ensure proper connection. It is not easy to cope with this task on your own, but if you follow the simplest rules, the result will not take long to arrive. How to connect the washing machine motor will be discussed later in the article.
Types of washing machine motors
The order in which the switching is carried out, as already noted, depends on the type of motor. Therefore, before activating it, you need to understand what type of mechanism we are talking about. It can be asynchronous, collector, inverter.
Asynchronous motor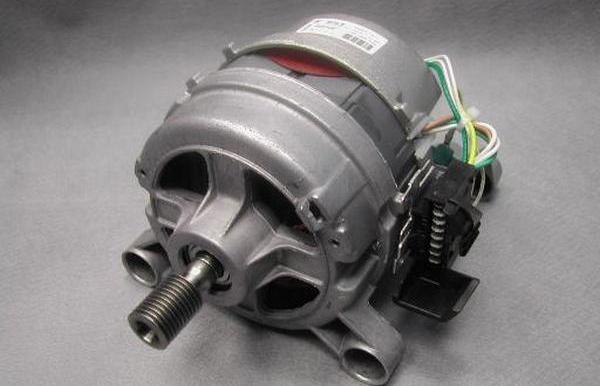
It was installed in units before the year 2000. The semi-automatic machine has 2800 rotations per minute when operating at a power of 180-360 W. To make such an engine suitable for “garage” options, you will need a three-phase network and a frequency converter. You also cannot do without a set of capacitors. Their cost is quite high, so motors of this type are the least in demand.But technical difficulties in its use are excluded due to the simplicity of the design and ease of maintenance.
The basic advantages of asynchronous motors are described above. As for the disadvantages, they can be described as follows:
- small sizes;
- low power;
- Difficulties in working with the engine.
It is for these reasons that the devices are not popular, and experienced owners of washing equipment prefer devices with other types of motors.
Brushed motor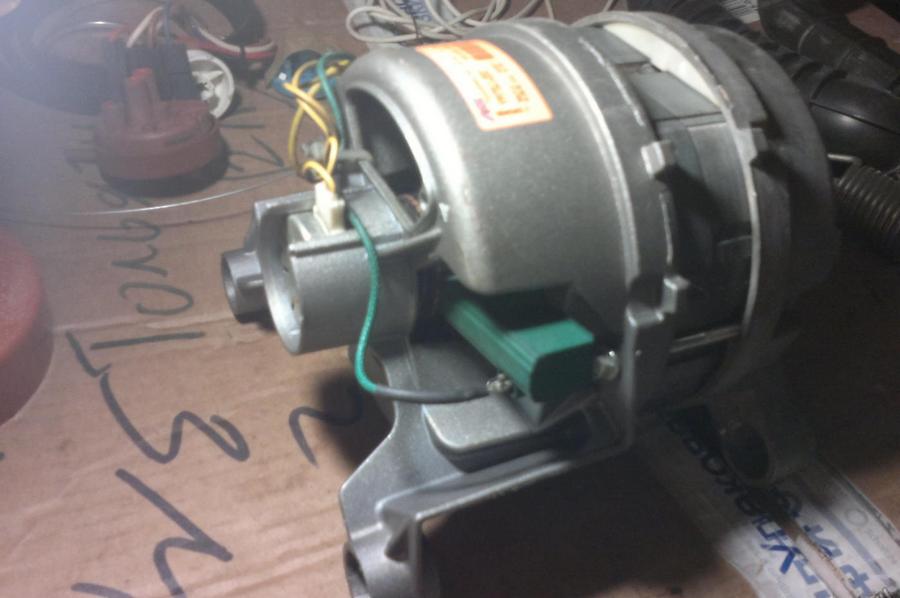
He is a real favorite among the masters. The device is capable of operating on direct and alternating current, the power value is 300-800 W, the number of armature turns is equal to up to 15,000 rpm. The advantages of models of this type include the following points:
- ease of cycle correction without compromising power;
- relatively low cost;
- high-torque;
- high speed of operation;
- ease of management work.
The main drawback is the brush assembly. The fact is that with an average load of the unit, it lasts no more than 10 years, and then needs to be replaced. Along with this, brushes are characterized by grinding.
Inverter motor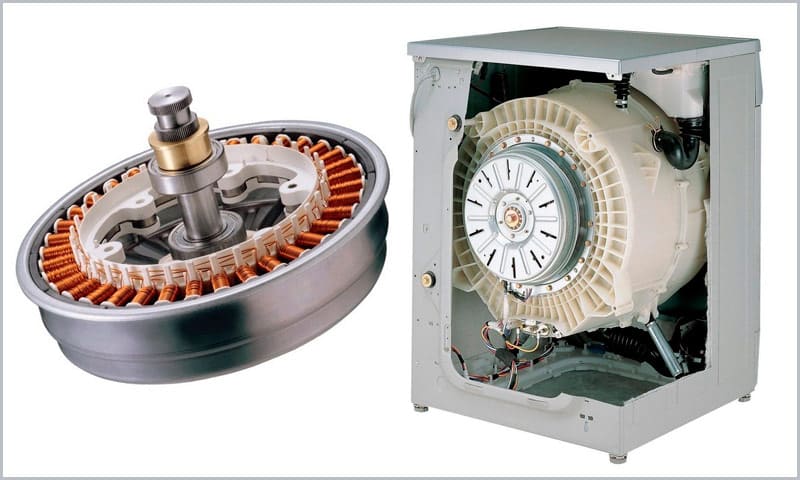
It is the most modern and is used in most progressive washing devices. Its task is to convert current. The operation does not require a belt drive and brushes, the power level is 400-800 W, the number of revolutions reaches up to 20,000. To activate this mechanism, you do not need to use capacitors; it is possible to change the direction of rotation. The operation is silent and there are no vibrations.
The disadvantages include high cost and vulnerability to power surges in the network.
Connecting the motor of a modern washing machine to a 220 V network
We are talking mainly about commutator motors, which do not have a starting winding and a capacitor. Operation occurs due to direct and alternating current. The number of pins on the terminal device can reach 8 pieces, but they are not needed for the operation of the unit. The main thing you need to take care of is eliminating unnecessary contacts. In this case, the winding resistance level will be 60-70 Ohms.
Along with this, it is possible to eliminate the thermal protection output, which is quite rare. We are talking about a contact, closed (normally) or open, with zero resistance. After this, voltage is connected to one of the terminals. The second, in turn, is connected to the first brush. The second is activated with a 220 V wire.
After this, the motor should start working and rotate in one direction. To change the direction of movement of the device, the connection of the brushes must be swapped. If you activate this unit with a voltage of 220 V, it will start working abruptly, you can even prepare for a characteristic jerk. So, to avoid shorting the wires, you need to act gradually.
Connecting the motor of an old washing machine
Practice shows that old-style units are usually equipped with an asynchronous motor with two windings. One of them is working, while the second is starting. If, during the process of disassembling the engine, the home technician sees all the contacts, the connection will not cause any problems or difficulties: it will be enough to use a capacitor with a voltage of up to 600 V and a capacity of up to 8 μF.
To start the work process, you need to get a tester or multimeter. You will need to find two pairs of pins that completely match each other. Next, using the tester probes, you can find the wires connected to each other. To do this, you need to activate the resistance mode when dialing.
The next step is to understand which winding is the starting winding and which is the working winding. All that remains is to measure the level of their resistance: if it is high, this indicates that the element is a starting element, it is responsible for creating torque at the start. If it is low, we are talking about the working winding, which forms a magnetic field of rotation.
Instead of an “SB” type contactor, a non-polar type capacitor can be installed, which is characterized by a minimum capacitance of 2-4 µF. If the engine is started without load, it can start itself without using a capacitor. If overheated, there is a possibility of bearing wear or a reduction in the size of the gap between the rotor and stator. But most often this happens due to the increased capacitance of the capacitor, so it is advisable to reduce it to the minimum level.
At the moment when the launch occurs, the “SB” button is pressed until the shaft spins up, this is usually no more than two seconds. After this, the button is lowered and the voltage supply stops. If reverse is needed, the winding contacts will need to be changed. In some situations, such a motor may have only three wires. In this situation there is a connection of two windings at the midpoint.
There is one more important nuance: if the motor does not use a starting-type winding, the direction in which rotation is observed can be any (absolutely in any direction). It most often depends on the direction in which the shaft is turned at the moment the voltage is activated.
Additional tips for work
When interacting with electrical systems, it is necessary to strictly observe safety rules, and also monitor the condition of the ends of the wires to avoid short circuits. In order for the engine starting work to be carried out at a decent level, you need to acquire certain accessories in advance:
- the wire;
- switch;
- plywood in several layers with a total thickness of 10 mm;
- bolts equipped with a head;
- screws;
- a block of wood measuring 40*40 mm;
- screwdriver;
- drill;
- screwdriver;
- hammer;
- an ordinary ruler with a pencil;
- pliers;
- grinder or saw with discs.
With these tools you can make a good circular saw. Of course, this will require some investment of time and money, but the result will be completely worth it. It is necessary to produce a separate unit, which is subsequently installed on a workbench with a high-power motor. The ability to instantly replace a disk plays an important role.
The motor with which the automatic washing machine is equipped is characterized by an extremely high rotation speed, so it is advisable to provide a regulator that will allow it to operate at different speeds without significant overheating. To solve this problem, a relay can be used in a classic or slightly modified form.
At the first stage, the triac along with the radiator is removed from the washing machine.It is a semiconductor device, in simple terms, a controlled switch. Subsequently, it must be soldered into the area of the relay chip, replacing parts with low power.
If you do not understand the basic nuances of the equipment, you should contact the service center to ask a specialist for help.
What to do if the engine does not start?
In some situations, the motor cannot be started, and there are several reasons for such difficulties (traditionally, these are mechanical and electrical problems):
- heating of the electric motor during switching on and the simultaneous lack of rotation of the shaft (instead, there is a grinding sound of metal parts, which indicates damage to the bearings that need to be replaced);
- accumulation of foreign objects in the area between the rotor and the starter, to solve the problem, you just need to remove all unnecessary and repeat the starting procedure;
- if you ring the entire network using a multimeter, you can determine a break, in collector motors, the brushes can also wear out, which prevents them from tightly adhering to the collector and generating energy;
- most often, after three minutes of operation of the motor, its heating is uneven, on the basis of which it is possible to determine the location of the breakdown and identify its causes;
- Often, the expansion of the capacitor capacity leads to malfunctions.
In addition, there are several more actions that need to be taken in a situation where the motor refuses to work. However, in practice, they are rarely used.
What can be made from an old washing machine motor?
Before deciding what can be made from old washing equipment, it is necessary to disassemble it.After prolonged exposure to water, a coating of salt may remain on it; it must be removed very carefully to avoid damage to spare parts. For homemade devices, a motor is often used, which acts as the basis of most devices. A drum is often used, which is usually made of stainless steel. The pipes are disconnected from it. Sometimes the hatch, springs, and other body elements may be involved.
Here are just some basic ideas for what can be made from an old washing machine engine:
- sharpener;
- grinding device;
- lathe;
- feather removal machine for household use;
- lawnmower;
- livestock feed cutter;
- generator;
- concrete mixer;
- circular saw (special saw).
From the drum you can make decorative devices, a barbecue and even a smokehouse. The procedure for manufacturing decorative and functional units depends on the specific idea and the method of its implementation.
Conclusion
Starting the engine of an automatic washing machine is a serious and responsible undertaking. However, with the right approach, even an inexperienced master can cope with this task. The main thing is to take precautions and follow the instructions.
In general, automatic washing machines are sold with different types of engines, and with the passage of time and the development of technical progress, their characteristics change. For this reason, the process for launching them may not be the same. The easiest way is to follow the recommendations described in the operating instructions, or contact a service center where workers will carry out all the necessary work.